1. Design & Engineering
a. CAD Modeling & Simulation
Engineers use CAD (Computer-Aided Design) software (e.g., SolidWorks, CATIA, or Siemens NX) to create 3D models of the mold.
CAE (Computer-Aided Engineering) tools simulate injection molding processes to predict flow, cooling, and potential defects (warping, sink marks, etc.).
b. Mold Flow Analysis
Software like Moldflow (Autodesk) analyzes:
Plastic flow behavior
Cooling efficiency
Potential air traps or weld lines
Optimizes gate locations, cooling channels, and ejection mechanisms.
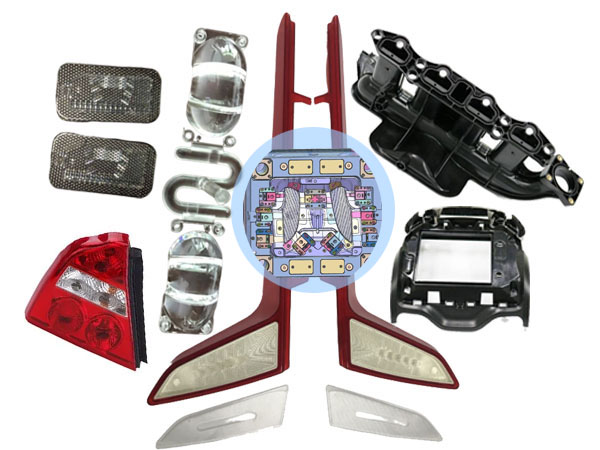
2. Mold Manufacturing (CNC Machining & EDM)
a. Material Selection
Common mold materials: P20 steel, H13 tool steel, stainless steel, or aluminum (for prototypes).
Hardened steels are used for high-volume production.
b. CNC Machining
CNC milling & turning shape the mold cavities and cores with high precision (±0.005 mm tolerance).
High-speed machining (HSM) ensures smooth surface finishes.
c. Electrical Discharge Machining (EDM)
Used for intricate details and sharp corners.
Wire EDM cuts fine features, while sinker EDM shapes deep cavities.
d. Surface Finishing
Polishing & texturing (e.g., for leather-grain or glossy finishes).
Coating (DLC, TiN, or CrN) to enhance wear resistance.
3. Mold Assembly & Testing
a. Fitting & Alignment
Core and cavity inserts are assembled with guide pins and bushings.
Ejector pins, sliders, and cooling channels are installed.
b. Trial Injection Molding
Test runs with actual plastic material (e.g., ABS, PP, PC/ABS).
Adjustments made to:
Injection pressure & speed
Cooling time
Ejection mechanism
4. Production: Injection Molding Process
Once the mold is validated, mass production begins:
a. Plastic Pellet Feeding
Raw plastic granules are fed into the hopper of the injection molding machine.
b. Melting & Injection
The barrel heater melts the plastic (~200–300°C).
A screw mechanism injects molten plastic into the mold cavity under high pressure (500–2,000 bar).
c. Cooling & Solidification
Cooling channels inside the mold help solidify the part (cycle time: 15–60 sec).
d. Ejection & Finishing
The mold opens, and ejector pins push out the part.
Secondary operations (trimming, painting, or assembly) may follow.
5. Quality Control & Automation
a. Inspection Methods
CMM (Coordinate Measuring Machine) checks dimensional accuracy.
Vision systems detect surface defects.
Pressure & temperature sensors ensure process stability.
b. Industry 4.0 Integration
IoT-enabled molds monitor wear and predict maintenance.
Automated robotic arms handle part removal and assembly.
Real-time data tracking for traceability and process optimization.
Conclusion
The plastic automotive mold manufacturing process combines precision engineering, advanced machining, and smart automation to produce high-quality plastic parts efficiently. With advancements in simulation software, high-speed machining, and IoT integration, modern mold manufacturing ensures faster production cycles, reduced defects, and better cost efficiency for automotive applications.
Plastic automotive mold is a mold used to produce automobile related products. SOMETOOL(SAM Molds) is a manufacturer of automotive parts mold and plastic injection molding auto parts. If you need automotive mold and injection molding products, please contact us.