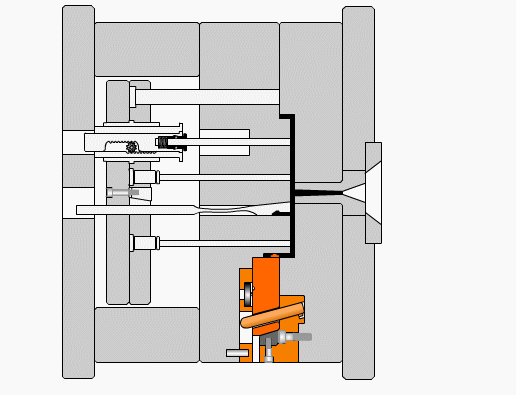
Plastic Injection Mold Producing
Precise mold design
● In-depth product analysis: fully understand the functions and performance requirements of injection molding products, accurately measure product dimensions, and control tolerances to the micron level. Use professional software to simulate and analyze the shrinkage rate and fluidity of products, consider the influence of factors such as material properties and molding process on product size and shape, and provide accurate basis for mold design.
● Optimize mold structure design: Adopt precise mold structure, such as hot runner system, to accurately control the flow of molten material, reduce material waste and molding defects, and improve molding accuracy. For multi-cavity molds, ensure the consistency of each cavity, adopt symmetrical layout and precise runner design, so that the molten material is evenly distributed to each cavity. At the same time, design reliable demolding mechanisms, such as precision ejector pins, push plate demolding, etc., to avoid damage or deformation of the product during demolding.
● Precise tolerance design: According to the product accuracy requirements, reasonably allocate the tolerances of each component of the mold. For key dimensions, such as cavity and core dimensions, the tolerance control should be strict, generally controlled within ±0.005mm, and the matching tolerance between the components should be considered to ensure that the mold accuracy meets the requirements after assembly.
Selection of high-quality mold materials
● High-purity and high-performance materials: Select high-purity mold steel, such as Sweden's ASSAB S136 and Japan's Datong NAK80. These materials have good mechanical properties, corrosion resistance and polishing properties, and can meet the requirements of high-precision injection molds. Its high purity and few impurities can ensure the dimensional stability and surface quality of the mold.
● Strict material inspection: Strict inspection of purchased mold materials. In addition to checking the conventional indicators such as hardness and strength of the materials, metallographic analysis and flaw detection are also required to ensure that the materials have no internal defects, uniform composition and stable performance.
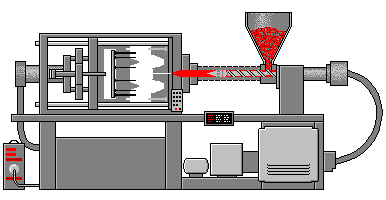
Plastic Injection Mold Principle
High-precision processing and manufacturing
● Application of advanced processing equipment: The five-axis linkage machining center is used for complex surface processing. Its high-precision positioning and linkage capabilities can achieve high-precision processing of mold parts, and the processing accuracy can reach ±0.002mm. Slow-feed wire cutting machine tools are used to cut high-precision mold parts, such as inserts, electrodes, etc., with high cutting accuracy and low surface roughness, which can ensure the dimensional accuracy and surface quality of parts.
● Precision grinding and polishing: Use precision surface grinders, internal and external cylindrical grinders, etc. to grind mold parts to ensure the dimensional accuracy and surface flatness of parts. For the mold surface, fine polishing is required, from rough polishing to fine polishing, gradually improving the surface finish, so that the mold surface roughness reaches Ra0.05 - Ra0.1μm to meet the molding requirements of high-precision products.
● Online measurement and compensation: During the processing process, online measurement technology, such as laser measuring instruments, contact measuring probes, etc., is used to monitor the size of parts in real time, adjust the processing parameters in time according to the measurement results, and perform error compensation to ensure that the processing accuracy of parts is always in a high-precision state.
Fine surface treatment
● Hard coating treatment: Physical vapor deposition (PVD) technology can be used to deposit hard coatings such as TiN and TiCN on the mold surface. The coating thickness is generally 1-5μm, which can effectively improve the mold surface hardness, wear resistance and demolding performance without affecting the dimensional accuracy of the mold.
● Chemical plating treatment: Through chemical plating of nickel-phosphorus alloy and other processes, a uniform and dense coating can be obtained, which improves the corrosion resistance and lubricity of the mold surface, is conducive to precision injection molding, and can ensure the flatness and finish of the mold surface.
Strict assembly and debugging
● High-precision assembly process: During the assembly process, high-precision assembly tools and measuring instruments, such as micrometers and optical centering instruments, are used to strictly control the assembly clearance and position accuracy of each component. For key matching parts, such as the matching of the cavity and the core, grinding and matching grinding are used to ensure uniform clearance, and the clearance is controlled within ±0.003mm.
● Multiple debugging and optimization: After completing the assembly, multiple trial mold debugging is carried out. After each mold trial, the mold and product are fully inspected to analyze product size deviation, surface quality and other issues. The mold is adjusted according to the problem, such as adjusting the mold gap, trimming the flow channel, etc. Through repeated debugging, the mold reaches the best molding state to ensure that the product accuracy meets the requirements.
Strict quality control
● Full process quality inspection: Establish a strict quality inspection system, from raw material entry inspection, part processing process inspection to mold assembly inspection, each link must be strictly controlled. Use a three-coordinate measuring instrument to measure mold parts and finished molds in all directions to ensure that the dimensional accuracy meets the design requirements.
● Statistical process control: Use the statistical process control (SPC) method to conduct statistical analysis on key parameters and product quality data in the mold manufacturing process, timely discover variations in the process, take measures to correct them, and ensure the stability and consistency of mold manufacturing quality.
SOMETOOL(SAM Precision Molds) is a professional manufacturer specialized in designing and manufacturing high quality plastic injection molds, die casting molds, CNC machined parts and injection molded components. Please contact us for you high precision molds.