1. Design Optimization
Simplify Part Design: Reduce complex geometries to minimize mold complexity and cycle time.
Use Uniform Wall Thickness: Ensure consistent wall thickness to avoid defects like warping or sink marks.
Incorporate Draft Angles: Add draft angles to facilitate easier ejection and reduce wear on the mold.
Design for Manufacturability (DFM): Collaborate with mold designers early to ensure the part is optimized for injection molding.
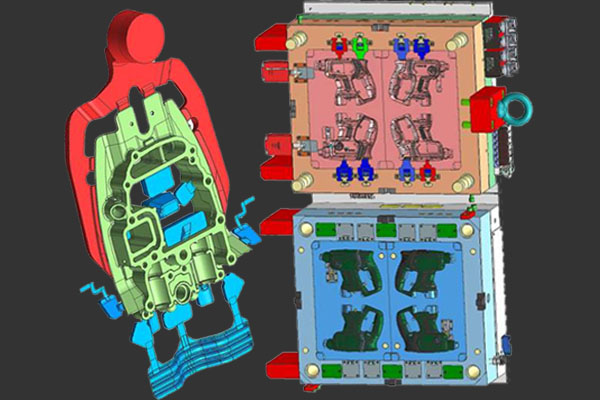
2. Material Selection
Choose the Right Material: Select materials that meet the part's functional requirements while being easy to process.
Use Recycled or Regrind Materials: Where applicable, incorporate recycled materials to reduce costs and environmental impact.
Optimize Material Flow: Ensure the material flows evenly through the mold to reduce defects.
3. Mold Optimization
High-Quality Mold Design: Invest in precision molds to reduce defects and improve part consistency.
Use Multi-Cavity Molds: Increase output by producing multiple parts per cycle.
Implement Hot Runner Systems: Reduce material waste and cycle time by using hot runner systems instead of cold runners.
Regular Mold Maintenance: Clean and maintain molds to prevent downtime and ensure consistent quality.
4. Process Optimization
Optimize Cycle Time: Reduce cycle time by adjusting injection speed, pressure, cooling time, and clamping force.
Automate the Process: Use robotics for part removal, sorting, and packaging to increase efficiency and reduce labor costs.
Implement Scientific Molding: Use data-driven approaches to monitor and control the injection molding process for consistency.
Minimize Scrap and Rework: Identify and address the root causes of defects to reduce waste.
5. Equipment Upgrades
Use Energy-Efficient Machines: Invest in modern injection molding machines that consume less energy and offer better control.
Implement Advanced Controls: Use machines with real-time monitoring and feedback systems to maintain process stability.
Upgrade Auxiliary Equipment: Ensure ancillary equipment (e.g., dryers, chillers, conveyors) is efficient and well-maintained.
6. Quality Control
Implement In-Process Inspections: Use sensors and cameras to detect defects during production.
Conduct Regular Testing: Perform quality checks on materials, molds, and finished parts to ensure compliance with standards.
Use Statistical Process Control (SPC): Monitor key process variables to identify and correct deviations.
7. Workforce Training
Train Operators: Ensure operators are skilled in machine operation, troubleshooting, and quality control.
Promote Continuous Improvement: Encourage employees to identify inefficiencies and suggest improvements.
8. Lean Manufacturing Principles
Reduce Waste: Eliminate unnecessary steps, materials, and downtime.
Implement Just-in-Time (JIT): Produce parts as needed to reduce inventory costs.
Streamline Workflow: Organize the production floor for efficient material and part movement.
9. Sustainability Practices
Reduce Energy Consumption: Optimize machine settings and use energy-efficient equipment.
Recycle Scrap Material: Reuse excess material and defective parts where possible.
Use Biodegradable or Recyclable Materials: Where applicable, choose eco-friendly materials.
10. Data-Driven Decision Making
Use IoT and Industry 4.0 Technologies: Implement sensors and data analytics to monitor machine performance and predict maintenance needs.
Track Key Performance Indicators (KPIs): Monitor metrics like cycle time, scrap rate, and machine uptime to identify areas for improvement.
By combining these strategies, you can optimize your plastic injection molding production, resulting in higher efficiency, lower costs, and better-quality products.