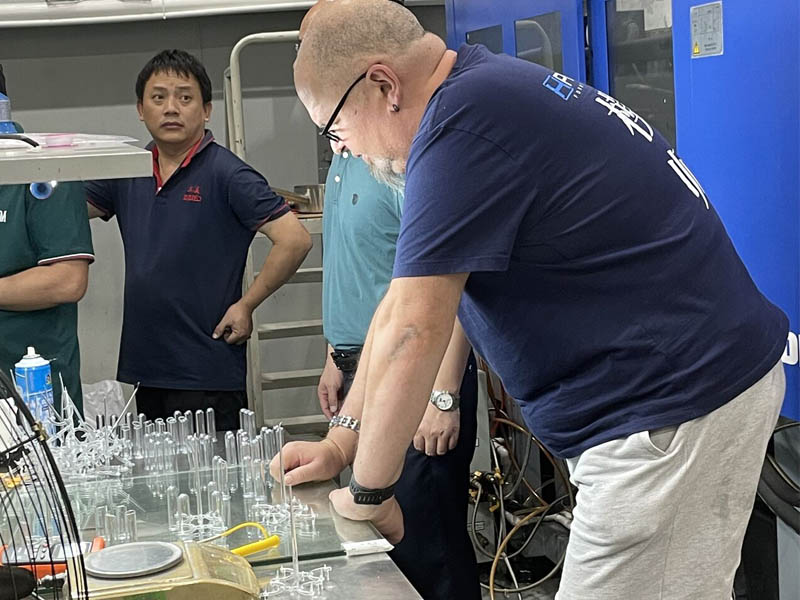
Following is a general outline of the steps involved in plastic injection mold inspection and acceptance:
1. Pre-Inspection Preparation
Review Design Specifications: Ensure that the mold design, including 2D drawings and 3D models, is thoroughly reviewed and understood.
Check Material Compliance: Verify that the mold material meets the required standards (e.g., hardness, corrosion resistance).
Inspection Tools: Prepare necessary inspection tools such as calipers, micrometers, CMM (Coordinate Measuring Machine), and optical comparators.
2. Dimensional Inspection
Critical Dimensions: Measure critical dimensions of the mold cavities, cores, and other components to ensure they match the design specifications.
Tolerances: Check that all dimensions are within the specified tolerances.
Surface Finish: Inspect the surface finish of the mold to ensure it meets the required roughness (e.g., Ra value).
3. Functional Testing
Mold Assembly: Assemble the mold and check for proper alignment and fit of all components.
Ejection System: Test the ejection system to ensure it operates smoothly and without obstruction.
Cooling System: Verify that the cooling channels are free of blockages and function as intended.
Venting: Check that the venting system is adequate to prevent air traps during injection.
4. Trial Production (Mold Testing)
Injection Molding Trial: Conduct a trial run using the intended plastic material to produce sample parts.
Part Quality: Inspect the molded parts for defects such as warping, sink marks, flash, or short shots.
Dimensional Accuracy: Measure the dimensions of the molded parts to ensure they meet the product specifications.
Cycle Time: Evaluate the cycle time to ensure it aligns with production requirements.
5. Documentation Review
Inspection Reports: Review all inspection reports and test results to ensure compliance with standards.
Certifications: Verify that the mold manufacturer has provided all necessary certifications (e.g., material certificates, heat treatment reports).
Mold Manual: Ensure that the mold manual, including maintenance and operation instructions, is provided.
6. Final Acceptance
Quality Approval: Obtain approval from the quality assurance team or relevant stakeholders.
Non-Conformance Resolution: Address any non-conformances or defects identified during inspection and testing.
Sign-Off: Complete the acceptance process with a formal sign-off document.
7. Post-Acceptance Activities
Mold Storage: Store the mold in a controlled environment to prevent damage or corrosion.
Maintenance Plan: Develop a maintenance plan to ensure the mold remains in good condition for future use.
Training: Provide training to operators and maintenance personnel on proper mold handling and maintenance.
Key Considerations
Communication: Maintain clear communication with the mold manufacturer throughout the process.
Standards Compliance: Ensure compliance with industry standards such as ISO 9001 or specific customer requirements.
Continuous Improvement: Use inspection data to identify areas for improvement in future mold designs or manufacturing processes.
By following these steps, you can ensure that the plastic injection mold meets the required quality standards and is ready for efficient and reliable production.
If you have needs in plastic injection mold processing, mold testing, please contact us for immediate support and consultation at:
Address: NO.45, Jinghai East Rd, Shatou Community, Changan town, Dongguan City, Guangdong Province, 523863, China.
Email: [email protected], [email protected]
Mobile: +86 13421913167