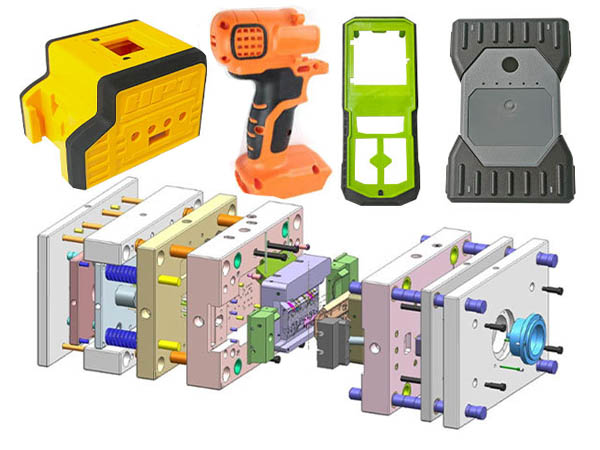
Processing Steps
1. Material Preparation
Select compatible materials (often a rigid plastic + soft TPE/TPU)
Dry materials as required (typically 2-4 hours at recommended temperatures)
2. Machine Setup
Use a specialized 2K injection molding machine with two injection units
Configure proper temperature profiles for each material
Set up the rotating mold or transfer system
3. First Shot Injection
Inject the first material (usually the rigid substrate)
Maintain proper injection speed, pressure, and cooling time
4. Mold Rotation/Transfer
Rotate the mold 180° (for rotary systems) or transfer the substrate to the second cavity
Ensure proper alignment and timing
5. Second Shot Injection
Inject the second material (often the soft overmold) onto the first shot
Control bonding interface temperature for optimal adhesion
6. Cooling and Ejection
Allow complete cooling of both materials
Eject the finished part
Key Process Parameters to Control
Temperature: Both material melting temps and mold temps
Injection Speed: Typically slower for the second shot
Cooling Time: Critical for part quality and cycle time
Clamping Force: Must be sufficient for both shots
Common Applications
Soft-grip handles
Sealed components
Multi-color parts
Overmolded electronics